|
PART FOUR
STRESS, STRAIN AND DISPLACEMENT RELATIONSHIPS FOR OPEN AND CLOSED SINGLE CELL THIN WALLED BEAMS
Assumptions:
1) Axial constraint effects are negligible
2) Shear stresses normal to surface can be neglected
3) Direct and shear stresses on planes normal to surface are constant across thickness
4) Beams have uniform section, with skin thickness varying around the section but constant along length of the beam
The parameter 's' in this analysis is the distance measured around the cross-section of the tube/beam from some convenient origin.
For a loaded beam, look at an element of size ds x dz x t of its wall showing all shear and direct stresses necessary to keep it in equilibrium.
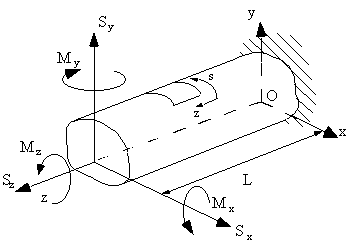
|
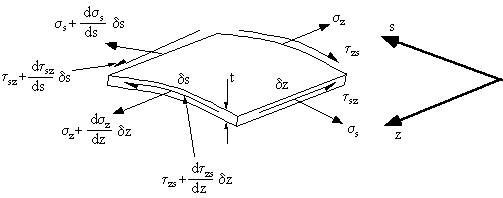
|
Figure 23: Loaded beam structure. |
Figure 24: General stress system on element of closed or open beam section. |
These shear and direct stresses are produced by the bending moments, shear loads and internal pressures. Although 't' can vary with 's' for each element of length ds, we can assume that this length is small enough to make 't' constant over this length.
From Elasticity we have that:

Instead of using shear stress, the analysis will become easier if we introduce the term Shear Flow q , which is the shear force per unit length rather than shear stress. It is represented by:
(4.1)
Shear flow is defined positive if it is in the same direction as increasing 's'.
What we are attempting to determine in this analysis are two things, firstly a relationship between the shear and direct stresses, and secondly a relationship between shear strain and the deformation of this element. So we may then use these relationships to determine a shear flow equation and an angle of twist equation.
We now replace the shear stress values in the element with those of shear flow:
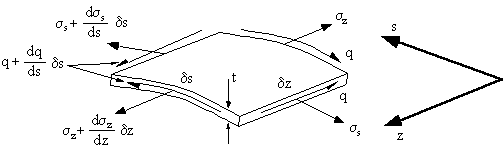
|
Figure 25: Element showing the direct stresses and shear flow. |
Using equilibrium about the z-axis and neglecting body forces gives:

Dividing by dz and in the limit as dz 0, it simplifies to:
(4.2)
and using equilibrium about the 's' direction Equation (4.3) is similarly derived.
(4.3)
We now need to look at strain relationships. Starting by defining the three components of displacement at a point on the tube wall.
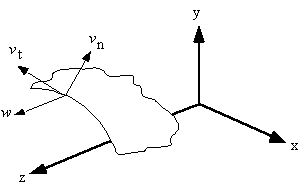
|
Figure 26: Axial, tangential and normal components of displacement of a point in beam wall. |
Where :
w = displacement in the z axis
vt = tangential displacement, positive with increasing 's'
vn = normal displacement, positive outwards
From Elasticity :
(4.4)
To define Shear strain look at how the element is distorted by shear:
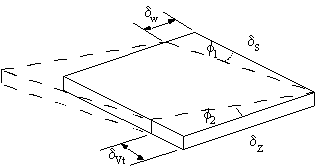
|
Figure 27: Element distorted due to shear. |
Shear strain is then defined as the addition of the two angles of rotation of the sides, such that:

where in the limits as the element size goes to zero:
(4.5)
It is now necessary to define the term vt as a function of displacements u and v ( in x and y axis)
and angle of twist of the section q. In order to do this it is necessary to assume that the ribs are able to hold the cross section rigidly enough so that when it twists it holds its cross sectional shape. However the ribs have no strength in a plane normal to them, allowing the section to warp or deform in the z axis.
Define
y = Angle between the tangent to the surface of the beam's cross section and the x-axis.
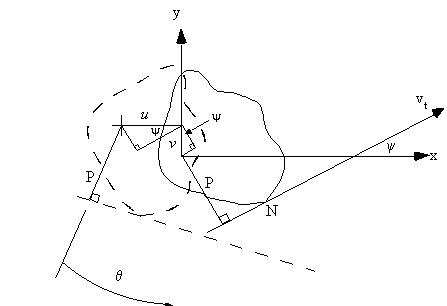 |
Figure 28: Beam cross section rotated by angle q, showing the rotation of the normal to surface. |
Tangential displacement at any point N on the tube is :
Relating these displacements about a point R, which is the centre of twist gives:
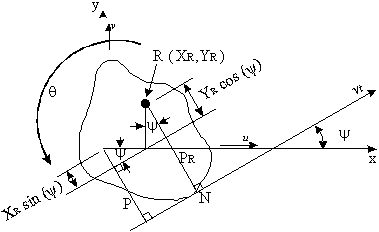 |
Figure 29: Rotation of beam section about centre of twist |
the displacement vt is

and

which when combined give:

These two equations which describe the tangential displacement of the tube. In order to determine the second term of Equation (4.5) it is necessary to differentiate Equations (4.6) and (4.7) with respect to z.
(4.8)
and
(4.9)
These two equations represent the same value, therefore the centre of rotation is:

These equations will be to use to determine the shear stress distribution in a thin walled open or closed tube, as well as the displacement, warping and angle of twist of the section due to these shear loads.
SHEAR FLOW IN BEAMS WITH OPEN SECTIONS
Look at a beam with an open section, with applied shear forces Sx and Sy about a point which produces no twisting of the tube cross section (Shear Centre).
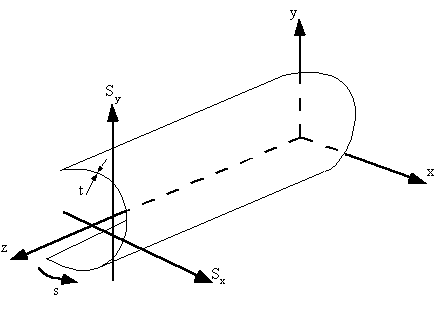
|
Figure 30: Open beam section loaded with two shear loads (Sy and Sx) |
The relationship between shear flow and axial stress is given by Equation (4.2):
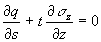
and the equation for direct stress is given by equation (3.11):
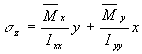
differentiating this equation gives:
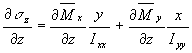
substituting back into the first equation gives:

substituting for the effective shear forces gives:

Integrating this equation wrt 's' from one point to another along the beam surface gives:

But by starting at s = 0 where q = 0 for an open beam, then:
Example 2: Determine the shear flow distribution in the thin walled channel section loaded
by a single vertical force applied through the shear centre.
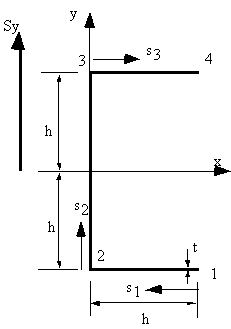
|
Figure 31: Channel section loaded vertically through shear centre. |
Since the applied vertical load passes through the shear centre, there is no torque applied to the beam, so shear flow equation (4.13) applies.
Since only Sy is applied, then:

Where :
, , 
Which gives that
, 
So equation (4.13) becomes:

On the bottom flange 12, at s1 = 0, y = -h and at s1 = h, y = -h which by using the equation of a line y = ms1 + b gives that: y = -h, where 0 < s1 < h so the shear flow between points 1 and 2 is:

giving:

Now at s1 = 0, q12 = 0, at s1 = h, q2 = 3Sy / 8h, and from equation (iii) it can be seen that we have a linear increasing shear flow.
On the web 23, at s2 = 0 , y = -h and at s2 = 2h, y = h which by using the equation of a line y = ms2 + b gives that y = - h + s2, where 0 < s2 < 2h , but at point 2 the shear flow is not 0 so:

giving:

Which has the form of a parabola symmetrical about the x-axis, with the maximum value of shear flow at s2 = h, of q23 = 9Sy / 16h, and at s2 = 2h, q3 = 3Sy / 8h.
On the top flange 34, at s3 = 0, y = h and at s3 = h, y = h which by using the equation of a line y = ms3 + b gives that y = h, where 0 < s3 < h so the shear flow between points 3 and 4 is:

giving:

And at s3 = h , q4 = 0, which is a linearly decreasing shear flow.
The shear flow distribution looks like this:
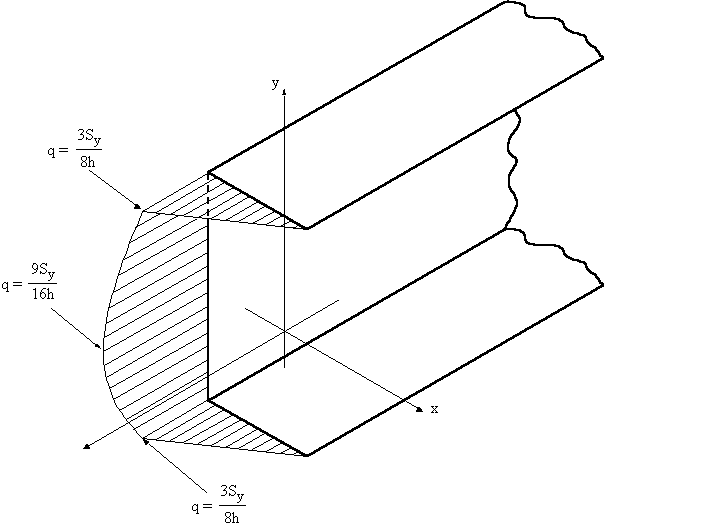
|
Figure 32: Shear flow distribution on channel section |
SHEAR CENTRE OF OPEN BEAM SECTION
The shear centre is that point in the cross section through which the shear loads produce no twisting. It is also the centre of twist when torsional loads are applied. As a rule, if a cross- section has an axis of symmetry, then the shear centre must lie on that axis and in cruciform or angle sections, the shear centre is located at the intersections. It is important to define the position of the shear centre because although most wings are not loaded at this point, if we know its location, we can represent the shear loads applied as combinations of shear loads through the shear centre and a torque.
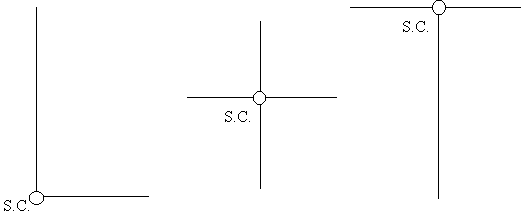
|
Figure 33: Shear centre locations for some typical open beam sections. |
To calculate the shear centre, determine the moment generated by the shear flow about an appropriate point in the cross section. This moment is equal to the moment generated by the applied shear force about this same point.

Example 3: For the open beam section of Example 2, determine the position of the shear centre.
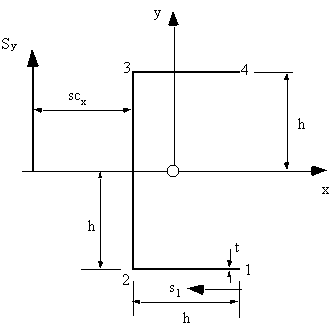
|
Figure 34: Channel section with load through shear centre. |
Because shape is symmetrical the shear centre must lie on the x-axis, a distance scx from the web.
The steps in determining the shear centre are as follows:
1) Determine the equations which describe the shear flow in the cross section, (done).
These were found to be:

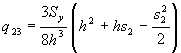
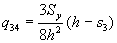
2) Find an appropriate point in the cross section and take moments about it. In this case
point 3. This eliminates the moments caused by the shear flow in the web 23 and flange 34.
The moment equation is:

substituting the equation for q12 defined previously, gives:

which gives:

Note: In the case of unsymmetrical sections, the coordinates (scx, scy) of the shear centre have
to be found. This is best achieved by first applying a vertical shear force Sy,
determining scx, then applying a horizontal force Sx determining scy.
SHEAR FLOW OF CLOSED TUBES
This solution is similar to that for an open beam section but with 2 differences:
1) Shear loads may be applied through any point in cross section;
2) At origin of 's', the value of shear flow qs,0 is unknown
Look at arbitrary closed beam, with applied shear forces Sx and Sy
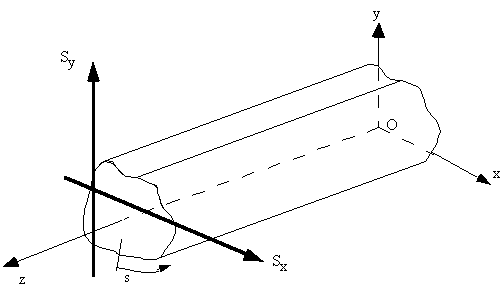
|
Figure 35: Closed beam section with two shear loads (Sy and Sx) |
If hoop stresses and body forces are absent, it is necessary to use equation 4.2:
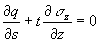
and as for the analysis of open beam sections, when substituting for sz, we obtained:

However unlike for open beams, at s = 0, qs0 0, so when integrating we get:

The first two terms are identical to the equation of shear flow of open tube loaded through shear
centre. If we let this terms be ‘qb’ then:

To obtain qb we assume the beam section is cut at some point to produce an open tube, and the shear flow distribution is then given by the following equation, which is equation (4.13).

where at s = 0 , qs = 0.
What is now required, is a way of determining the value of the shear stress at the point where the beam was cut.
To do this, look at beam cross section loaded at some point:
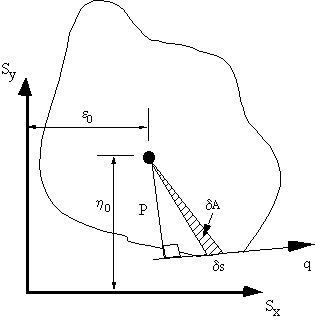
|
Figure 36: Resolving moments due to applied loads and shear flow about a point. |
Take moments about a convenient point inside the beam.
The moment equation will look like this

but the shear flow term is given by equation 4.16, so substituting for q gives:

The term is the integral around the cross section.
By looking at the area enclosed by the elemental distance s and the point where moments are taken, then:

Integrating this over the cross section as the element d s 0, gives:

Which means that:

where :
A = Area enclosed by the mid-line of the beam section wall
Giving that:

But if we take moments about the points where the shear forces are applied, then this equation becomes:

which can easily be used to determine the value of qs,0.
TWIST AND WARPING OF SHEAR LOADED CLOSED SECTIONS
If a shear load is not applied at the shear centre, the closed beam section will both twist and have an out of plane axial displacement (warp).
From equation (4.1) shear flow is defined as:

and from elasticity:

with the term for shear strain given by equation (4.5)

Combining all three equations gives:
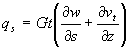
and substituting equation (4.8) gives:

Integrating this equation around the cross section wrt 's' gives:

Which is the rate of twist of the beam wrt z.
If however, equation (4.20) was integrated wrt 's' from some origin point on the surface of the beam to any other point in the cross section, with the axis origin at the shear centre, it gives:

where :

and

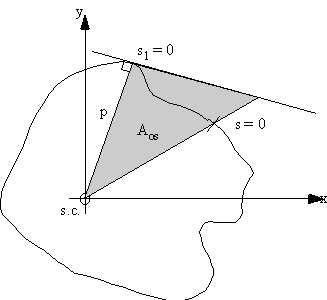
|
Figure 37: Beam section showing area swept by generator. |
This equation gives the axial displacement or warping of the beam. If the cross section was singly or doubly symmetrical, at the axis of symmetry the warping would be zero. If the origin of 's' was taken at any of these points then at s = 0, w0 = 0 and the rest of the warping would be easily found.
For unsymmetrical sections, the unknown warping displacement at s = 0 is given by:
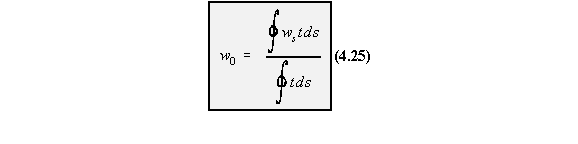
However in order to obtain these values, you must first know the position of the shear centre.
SHEAR CENTRE OF CLOSED BEAM SECTIONS
The position of the shear centre for a beam loaded as shown in Figure 38, can be found by using equation (4.17).

where:
ho = vertical distance from x-axis to shear centre from reference axis
eo = horizontal distance from y-axis to shear centre from reference axis
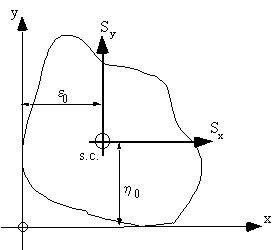
|
Figure 38: Determining location of the shear centre for closed beam section. |
In order to determine the shear centre we need to determine qs,0. From the definition for shear centre, if a shear load is applied here, it produces no twist, so by using equation (4.21) :

and substituting for qs,0 it gives:
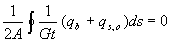
which gives that:
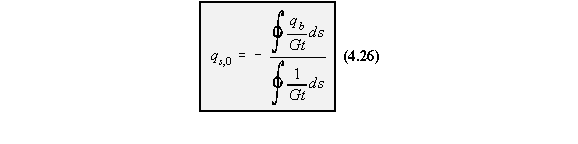
and if Gt is constant:

With these equations the shear flow , shear centre, the rate of twist, and warping in a closed beam section can now be determined.
Example 4: Determine shear flow, shear centre and warping in the following closed beam
section loaded with a shear force S y at the s.c.. G is constant .
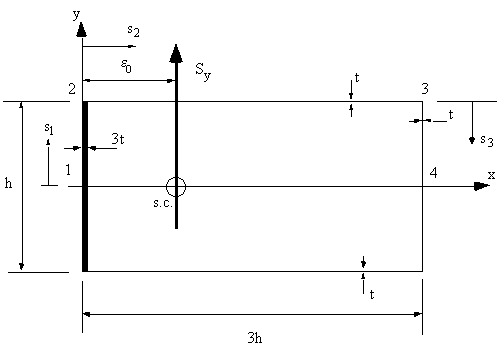
|
Figure 39: Closed section of question 5. |
1) Determine sectional properties
Since section symmetrical Ixy = 0, and since only loaded vertically , only need Ixx, which is:
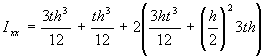
giving:

Therefore:
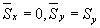
2) Determine Shear Flows
Between 1 and 2, y = s1 and at s1 = 0 , q1 = q0
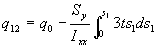
giving:

between 2 and 3, y = h/2, at s2 = 0, q2 = q0 - 9Sy/44h, giving:

between 3 and 4, y = h/2 - s3, at s3 = 0, q3 = q0 - 45Sy/44h, giving:

at s3 = h/2, q3 = q0 - 48Sy/44h
The shear flow distribution will look like this:
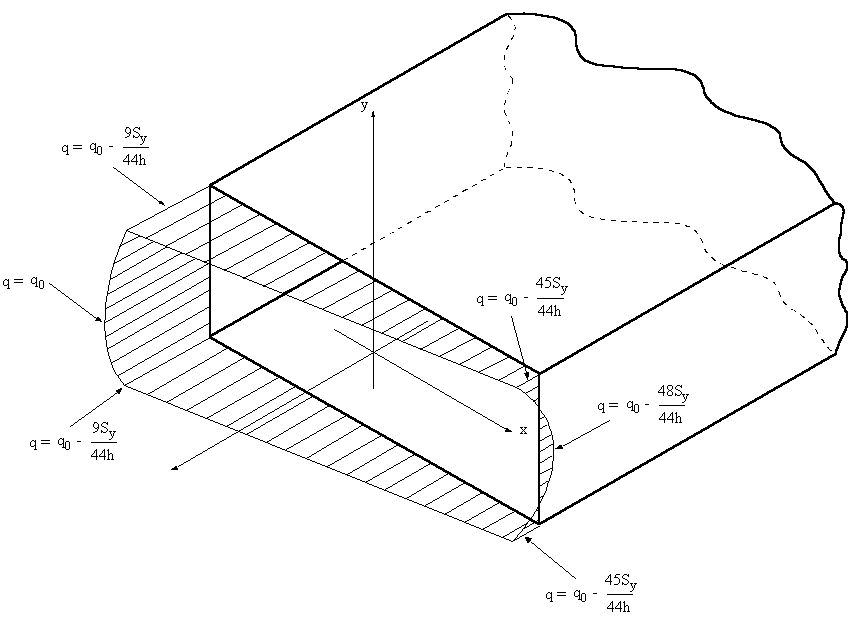
|
Figure 40: Shear flow distribution with constant q0 |
3) Determine q0
Because 't' is not constant, equation (4.26) becomes:

where due to symmetry:

and

giving that:

Substituting this into (i), (ii) and (iii) gives:
 

Plotting the shear flow distribution, it would look like this:
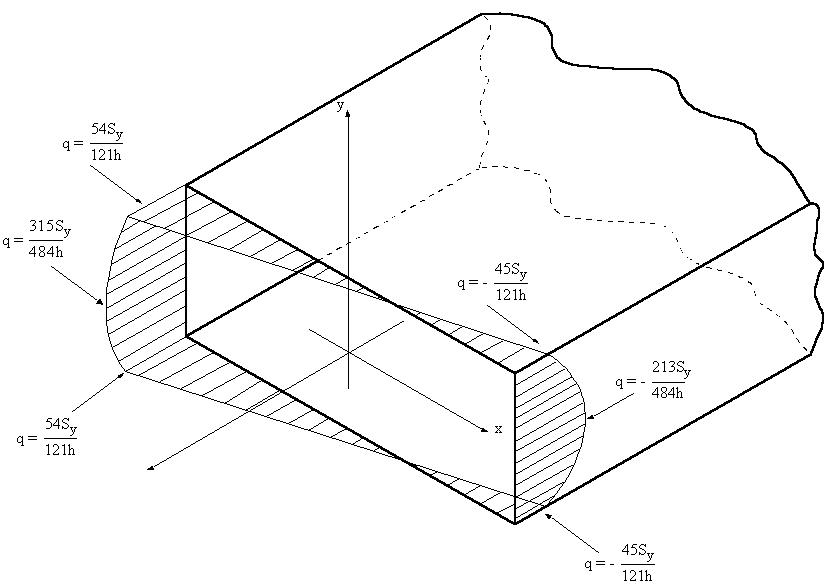
|
Figure 41: Shear flow distribution of closed beam. |
4) Determine Shear Centre
To determine the shear centre you can use equation (4.18 mod.) or since qs,0 was found, use equilibrium. If you use the latter it a lot easier.
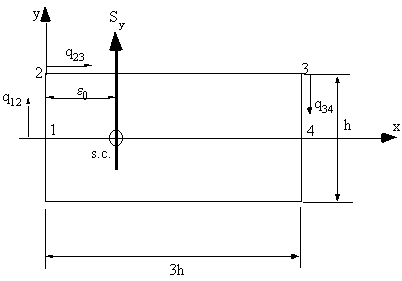
|
Figure 42: Closed beam indicating applied shear force and the direction of the shear flow. |
From definition of applied moments and resultant moments due to internal stresses:

Taking moments about point 1

First term:

Second Term:

Substituting into (vii) gives:

5 ) Determine Section Warping
This is done using equation (4.22) but first the axis must be moved to the shear centre:
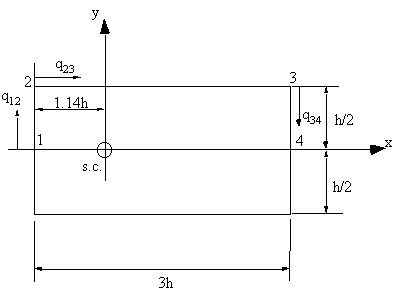
|
Figure 43: Closed beam with axis shifted to shear centre. |
Since our origin is point 1, the at s = 0 , w0 = 0, so equation (4.22) becomes:

But because the load is applied through the shear centre, the right hand term goes to zero, giving that

Between 1 and 2,

At point 2,

and between 2 and 3,

at point 3,

and between 3 and 4

Because the section is symmetrical about the x-axis, the warping distribution is equal in magnitude but opposite in direction. If this is plotted, it looks like this:
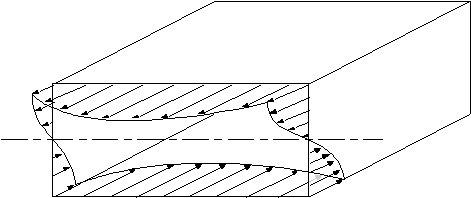
|
Figure 44: Diagram showing the warping distribution on the closed beam. |
...Back to Top |